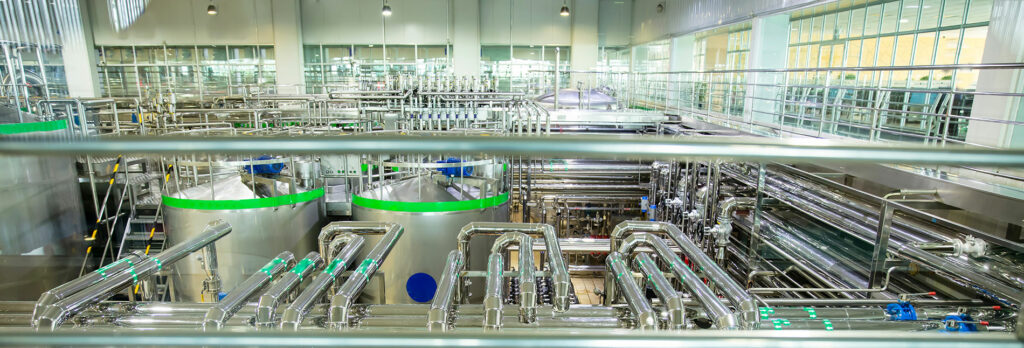
大手プロセス型精密機器製造業
大手プロセス型の工場において、AIアルゴリズムを用い、ミリ秒単位の時系列信号データの波形リアルタイム診断を工場ワイドに実装し、異常検知のほかロット間の差異の確認を行い、製造品質の向上を行いました。
課題の背景
従来から設置してあるセンサーでは、大まかな信号や数値しか取得できず、製造ロット間にばらつきがあっても、その原因を探求することができませんでした。また、製品搬送システムにおける重故障を予測することが難しく、工場全体において品質を脅かす監視体制に限界があったため、大量の製品や中間品を破棄する必要があり、歩留まりがなかなか向上しませんでした。
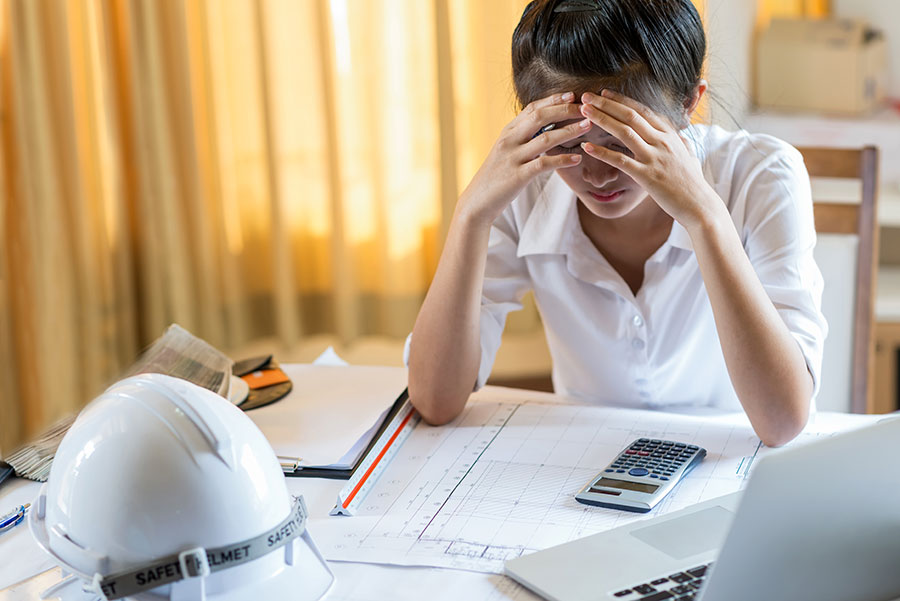
課題に対する施策
工場の操業を脅かす製品搬送システムなどのファシリティ設備の予防保全環境を整備することで、重故障を未然に防ぐ体制を整えるとともに、生産装置から排出される信号をまずは素直に観察する習慣を身に着けることで、工場全体が「データに基づく業務」に次第に変化していく文化を醸成することができました。各信号に適した監視ルールを使い分ける工夫も各種設備を通して培ったノウハウです。
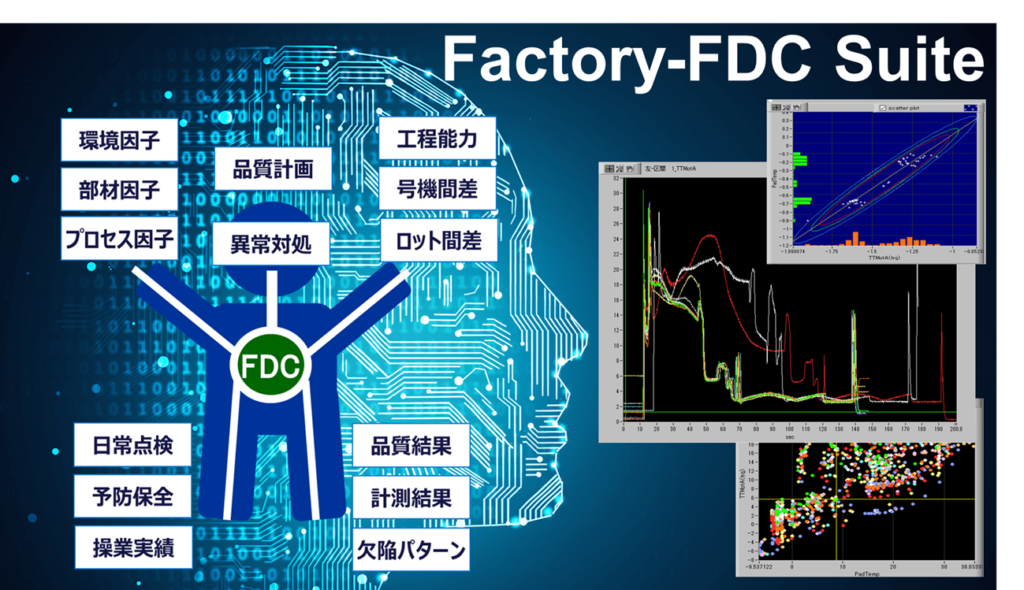
その後の変化
Factory-FDC Suiteを導入し、工場の各工程の状態を収集し、いつでも解析できるようにしました。これにより、一回のロット製造で収集するデータは、数百ギガバイトにおよび、故障モード影響解析(FMEA)に使用できる情報が格段に増えました。
トップダウンでは、重要インシデント対策と恒久対策としてのFMEAの再定義がスピードアップされ、深層要因の特定と再発防止がスムーズに進むとともに、ボトムアップでは製造システム間の因果関係などが現場でより詳しく把握できるようになりました。
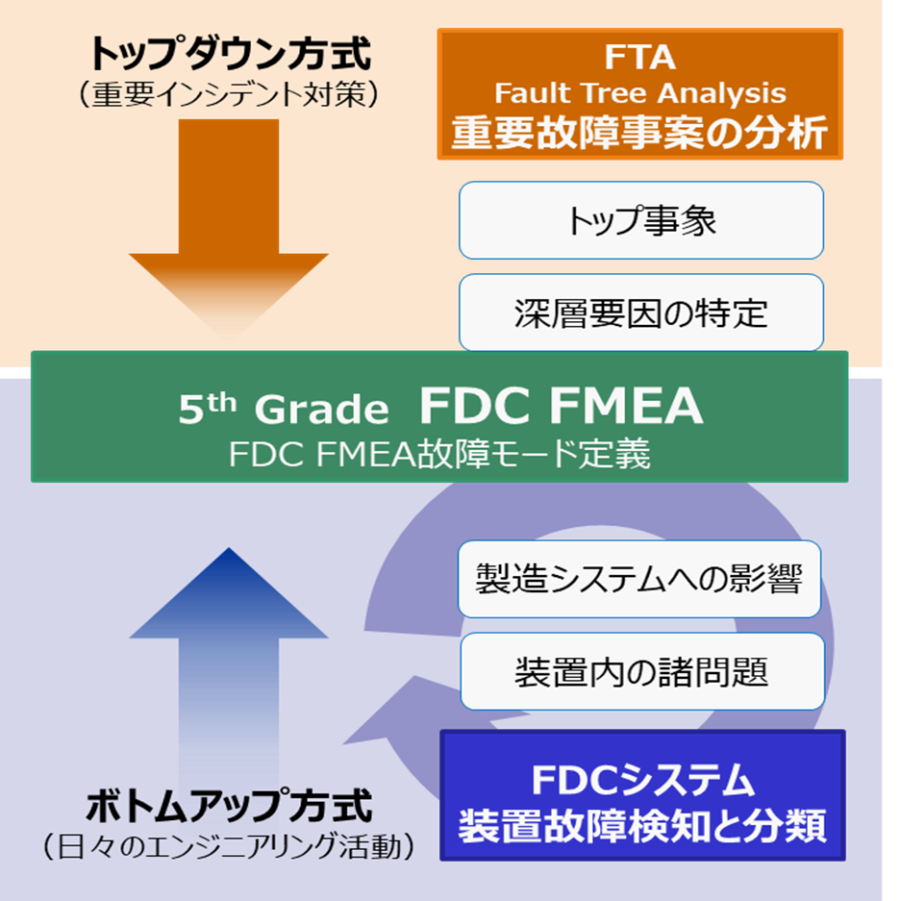