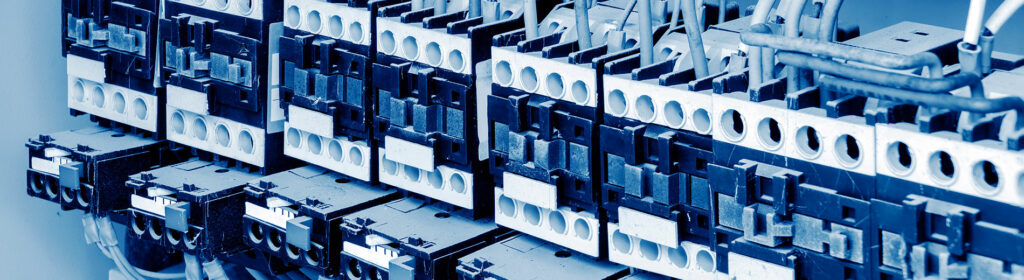
- 工場・施設データのリアルタイム異常検知と診断
工場操業データ解析
当社では、株式会社デュラシステムズが提供する製造ライン及び装置向け監視ツール「TDX」をエンジンとして採用し、この仕組みを工場ワイド・施設ワイドに実装し、AI・機械学習エンジンによる生産性最大化を推進するソリューションを提供しています。
特徴
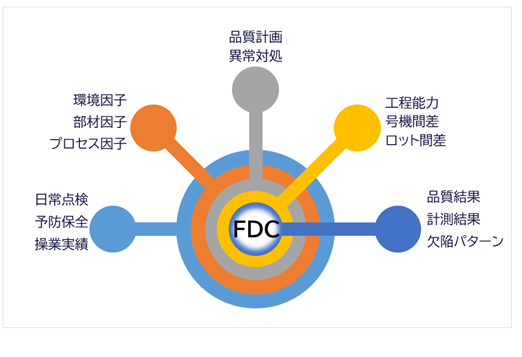
生産装置からミリ秒単位での生波形データを監視することにより、圧倒的な区間統計量を生み出すことができます。非線形AIアルゴリズムによる監視が可能ですので様々な異常を検知することができます。また、ペタバイト級のビッグデータを保存しておき、クラウドと連携して解析することが可能です。
- 装置、製造工程の詳細な IPO 情報を取り扱いながら、“数十倍もの優位な区間統計量を創出”
- 装置の内部状態を可視化させ、波形の特徴を踏まえた異常検出、異常予測の監視環境を提供
- 1マイクロ秒単位のデータ解析にも耐える高速処理
- 機械学習エンジンによる製造品質(良品空間)のモデル化を実現
- 長期品質トレーサビリティに耐えうるクラウド型データウェアハウス
利用例
具体的には、以下のような業務改善に寄与する仕組みを実現します。
多変量SPC監視の実現 : MSPC(Multivariate Statistical Process Control)
異常検知&分類の実現 : FDC(Fault Detection & Classification)
リアルタイム条件制御の実現 : APC(Advanced Process Control)
実際の工場では、操業・生産装置・加工ワーク品質をリアルタイムに監視し、装置の揺らぎを波形から検知しフィードバック修正することが可能となります。また、過去のトラブルや事象を自動監視モデルに追加することで、AI学習モデルがチューンアップできます。
または、装置チャンバー内での正味稼働状況を分析することができるようになるので、従来では不可能だった事象に対しても、多変量統計解析や多変量SPCなどのアプローチにより、製造品質問題を解決することが可能になります。
また複数波形をリアルタイムに描画することも可能です。これにより着目箇所を洞察し、監視モデルを検討することができます。しかも、1マイクロ秒単位のデータ取得と分析に耐える性能を持つので、振動波形など秒間 100万ポイントの取得を必要とするニーズにも応えることができます。
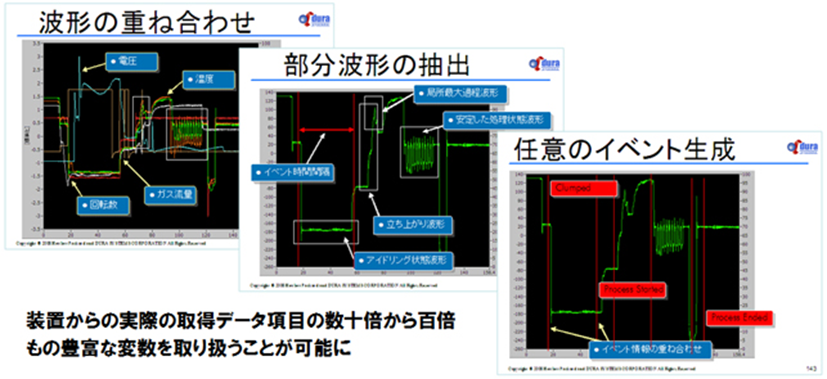
装置・要素技術開発フェーズ~装置やプロセスの瞬間立ち上げに向けて以下のような項目が可能になります。
(1) 装置の異常発生の前兆となるバラつきの検出
(2) 装置の正常範囲内であるバラつき幅の見極め
(3) 装置の変動因子や制御因子(重要パラメータ)の見極めと2次加工抽出
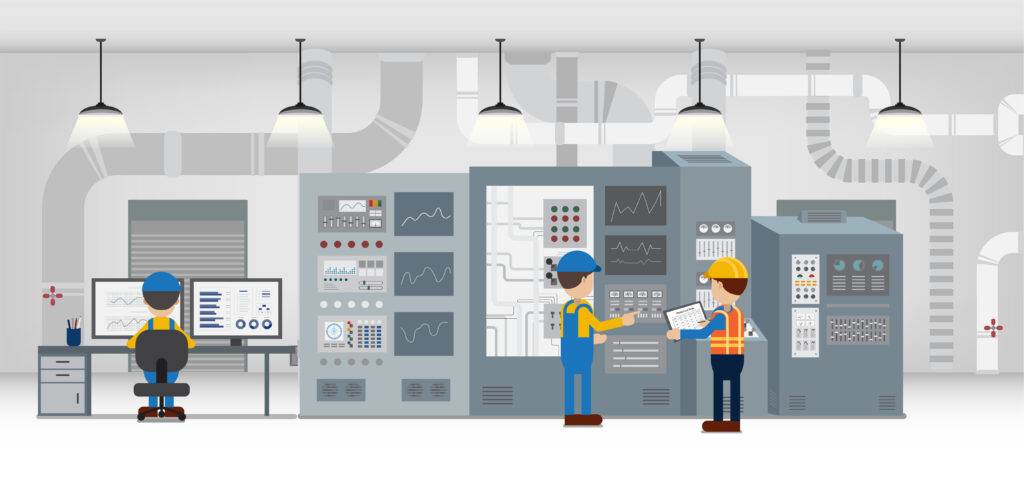
また、中量・量産フェーズ~工程の安定性確保、工程能力の改善に向けては、以下のような項目が可能になります。
(1) 装置異常の早期検出
(2) 装置セットアップ後の状態確認
(3) 装置間差の解析とBKM(best Known Method)の展開
(4) 装置保守の効率化。故障予測による不良品発生防止と予防保全
(5) 装置内部の稼働状態を詳細に把握することでスループット改善計画
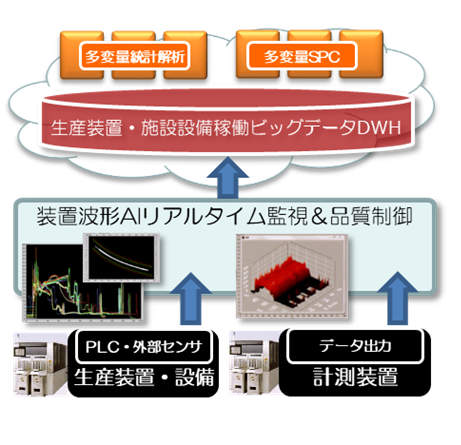
データ分析画面の一例を以下に示します。
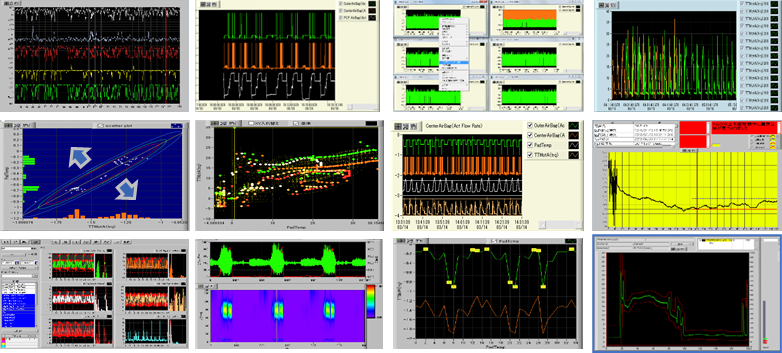